A magnifying lamp is an essential tool for anyone working with precision assembly, inspection or design. Because users can effortlessly view smaller details, lighted magnifying lamps are tremendously helpful in reducing eye strain and preventing vision fatigue. As a result, they are popular with jewelers, watch and electronics repair, dental clinics, industrial inspection, scientific research laboratories and the home office. This quick reference guide will boost your understanding and guide you to the magnifier which best suits your needs.
Do I need a “lighted” magnifier?
Good, clean lighting is an essential element to consider when choosing a magnifier. Many workplace locations have indirect and shadow-filled lighting conditions at best, resulting in marginal viewing performance. Lighted magnifiers compensate for this with a quality fluorescent, halogen or LED lighting element embedded around the viewing glass frame. Fluorescent lighting brings out clarity of view by shining a broad, cool and shadowless light. Halogen lamps will yield a warmer glow and heat up more quickly. LED lamps put out less lighting, yet tend to last much longer than either fluorescent or halogen bulbs.
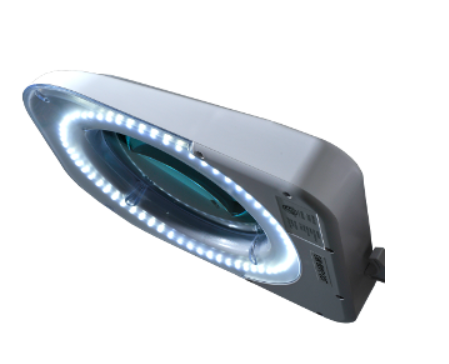
What does ‘Diopter’ mean?
When looking at various magnifiers, you’ll come across the term ‘diopter’. This refers to the amount of curvature a lens will have. More curvature means a thicker lens, more magnification and a higher diopter number. To find the magnification level of a lens, simply divide its diopter by 4, and add 1. For example, if you’re looking at a 3-diopter lens, it’s magnification = ¾ + 1… or .75 + 1 = 1.75x. Objects viewed under a 3 diopter lens will appear 175% bigger than normal. A 5-diopter lens = 5/4 + 1… or 1.25 + 1 = 2.25x. Objects viewed under a 5 diopter lens will appear 225% bigger than normal.
What does focal length mean?
Focal length is defined as the distance from the lens to the point where an object is in focus (focal point) and it becomes important if you need space above the object in which to work. It’s kind of like shining a flashlight on a dark wall. As you move the flashlight (magnifier) closer to the wall, you are reducing its distance (focal length). As you move the flashlight back from the wall, the distance (focal length) increases. Unfortunately, you can’t have lots of magnification and lots of room below the lens (focal length). If you need lots of space to work, you won’t have as much magnification available. If you don’t need much working space, you can get stronger magnification, and in fact, magnifiers with higher power are generally reserved for close-in inspection and measurement… 3 diopter = 1.75x magnification at 13” focal length 5 diopter = 2.25x magnification at 8” focal length 7 diopter = 2.75x magnification at 5.5” focal length As a general rule of thumb, when your magnification gets larger, your lens and focal length get smaller.

Operator tips
1. Use both eyes when using a magnifying lamp, just like you would use a comfortable pair of prescription glasses.
2. Make sure the lens is positioned to keep your object in focus, with your eyes are 8” to 10” away from the glass. This will give you the best magnification with the least amount of distortion.
3. For best results, keep your chair height and working surface positioned to maintain good posture. You shouldn’t be leaning away from the lens when viewing the object.
About Gordak
Foshan Gordak Electric Co., Ltd. located at Lecong 325 national way, Shunde, works under the principle of focusing on technical innovation and sincere service, meeting demands of the market. And for its developing strong strength, GORDAK has make a good tongue in the electronic field.
GORDAK make the customer number one and provide the customers with the quality, soldering station, SMD rework station, Ultrasonic Cleaner, power maintaining tools, well sold abroad including Southeast Asia, Middle East and West Europe, most of them passed the CE certification and Gordak is already a ISO9001: 2000 registered company.
If you are looking for a reliable merchandise of Magnifying Lamps, please contact us now!